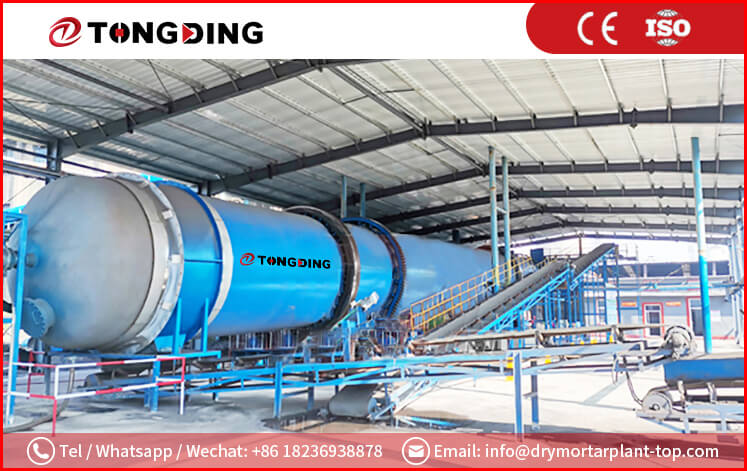
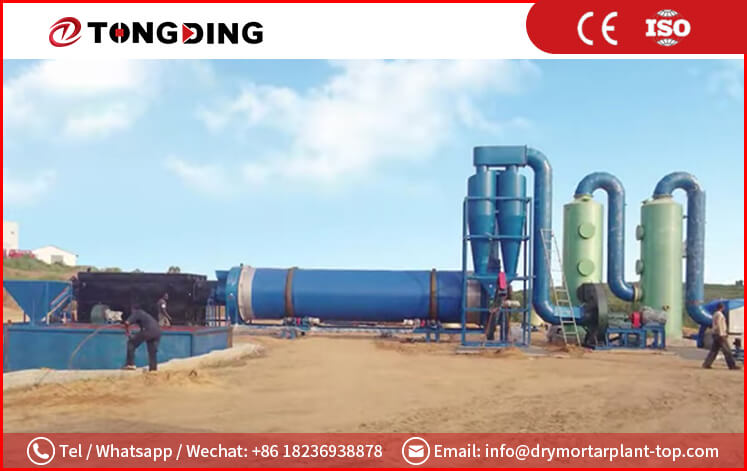
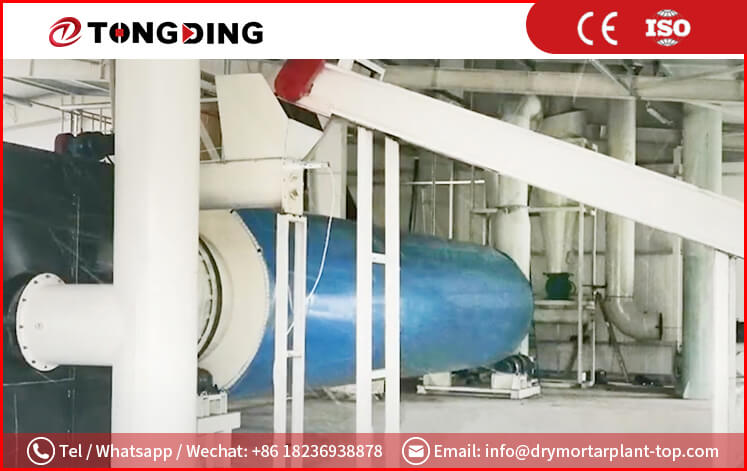
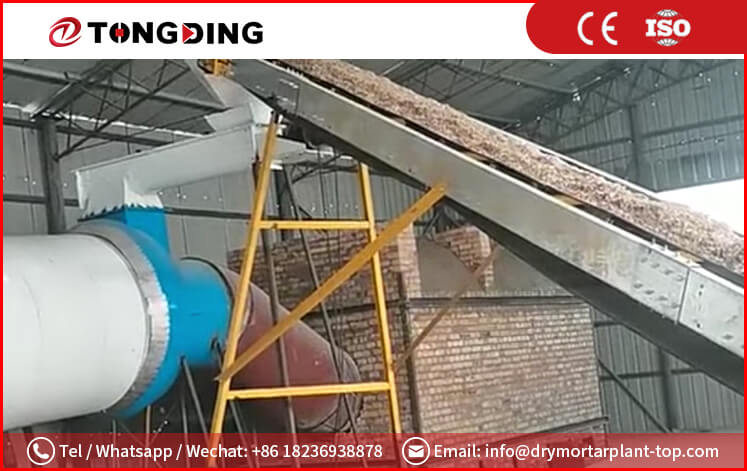
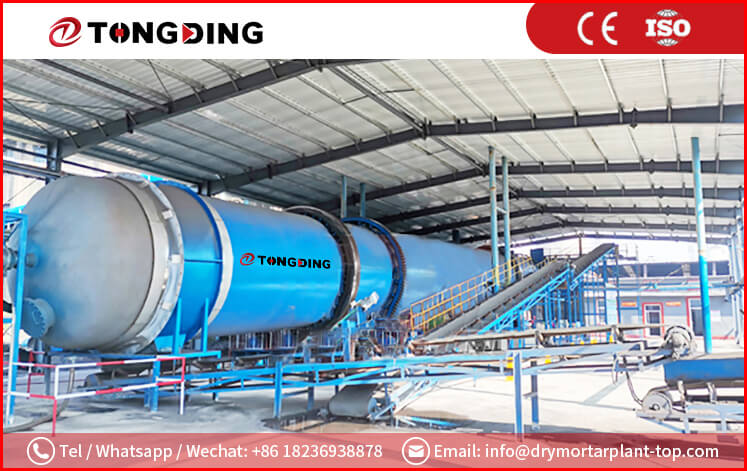
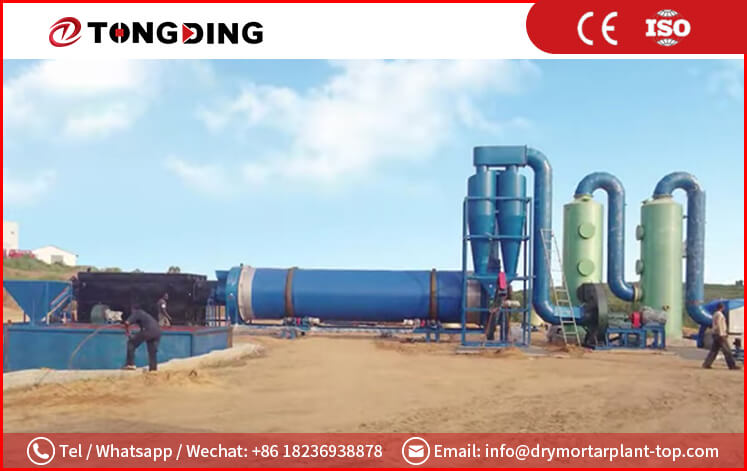
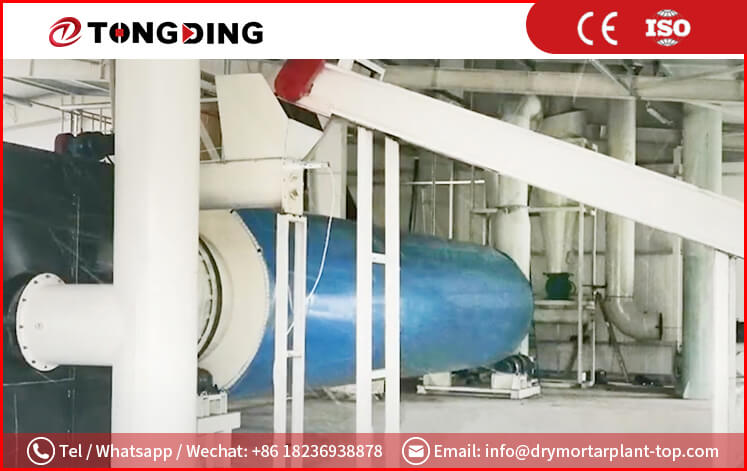
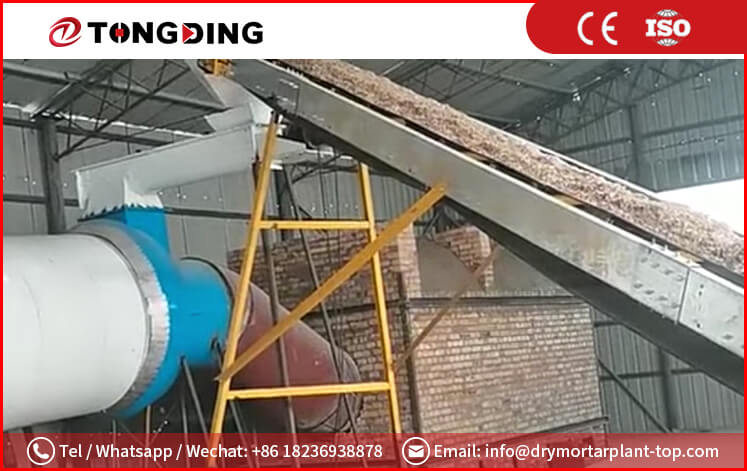
Steam Tube Rotary Dryer
Capacity: 17-400 t/d
Heat Source:Suitable for steam, biomass, natural gas, diesel, coal, etc.
Application: Widely used in the biomass, food, feed, fertilizer, bad slag chemical industry, medicine, coal, mining and other small particles or weakly caking dry powder material.
Product Introduction
The indirect heating mode of the drum dryer for oil heat (steam) drying involves the use of heat conduction oil or steam for drying. This type of dryer is characterized by low energy consumption, a safe drying process, and the absence of heat source pollution, making it widely utilized in various industries such as biomass, food, feed, fertilizer, bad slag chemical industry, medicine, coal, mining, and other applications requiring the drying of small particles or weakly caking dry powder material.
The heat conduction oil steam drum dryer is mainly composed of a tube type heat exchanger, center pipes for the inlet and outlet of the heat source, a rotary drum, a feeding and discharge machine, an induced draft fan, a dust collector, and distribution cabinets. The wet material is evenly distributed on the roller feed plate and column tube, which turn together and come into full contact with the hot conduction oil (steam) tube type heat exchanger, achieving heat transfer, mass transfer (at temperatures ranging from 110-250 ℃), constant temperature drying, water vaporization, and emission with the air. Gradually, the moisture content in the material is reduced until the drying process is complete.
This type of equipment is suitable for drying all kinds of coal, such as lignite, carbon coal, including anthracite, lean coal, and poor lean coal, coking coal, fat coal, air fertilizer coal, gas coal, and weakly caking coal, not sticky coal, long flame coal, lignite, coal washing, screening, raw coal, bituminous coal, the tail coal, midding coal, and others. The equipment can be customized according to the customers' requirements.
Layout Reference
Working Principle
The heat conduction oil steam drum dryer is primarily comprised of a tube-type heat exchanger, a center pipe for heat source inlet and outlet, a rotary drum, a feeding and discharge machine, an induced draft fan, a dust collector, and distribution cabinets. Upon entry of the wet material into the dryer, it is uniformly distributed onto the roller feed plate and within the column tube, which rotates as one. The wet material then makes full contact with the tube-type heat exchanger containing the hot conduction oil (steam). This contact results in heat transfer, mass transfer (110-250 ℃), constant temperature drying, water vaporization, and air emissions. As the moisture in the material gradually decreases, the material's drying process is completed.
Parameter
Model |
Capacity(T/D) |
Total Power(kw) |
Initial moisture(%) |
Final moisture(%) |
Drying temperature(℃) |
TDBPS40 |
15-40 |
20-28 |
35-50 |
12-15 |
110-250℃ |
TDBPS60 |
28-60 |
25-35 |
|||
TDBPS100 |
50-100 |
30-50 |
|||
TDBPS150 |
65-150 |
40-60 |
|||
TDBPS200 |
88-200 |
50-80 |
|||
TDBPS300 |
132-300 |
70-100 |
|||
TDBPS400 |
180-400 |
90-140 |
|||
Note: Increase the external fin tube heat exchanger of the dryer, drying capacity and water evaporation capacity increased 40-80%. |
Inquiry
Please Feel free to give your inquiry in the form below. We will reply you in 24 hours.