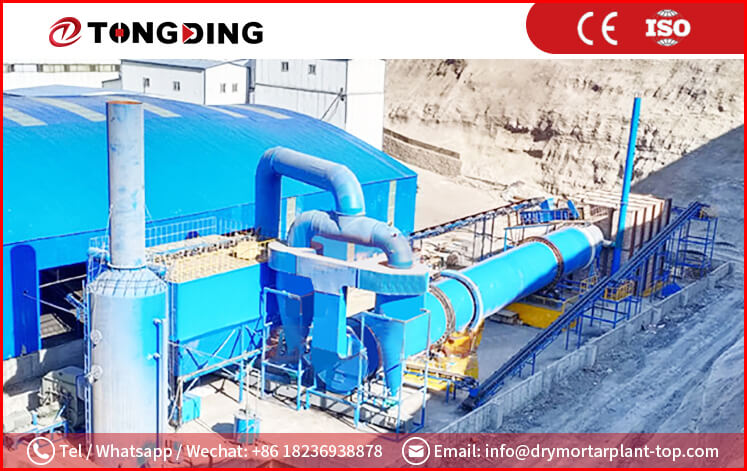
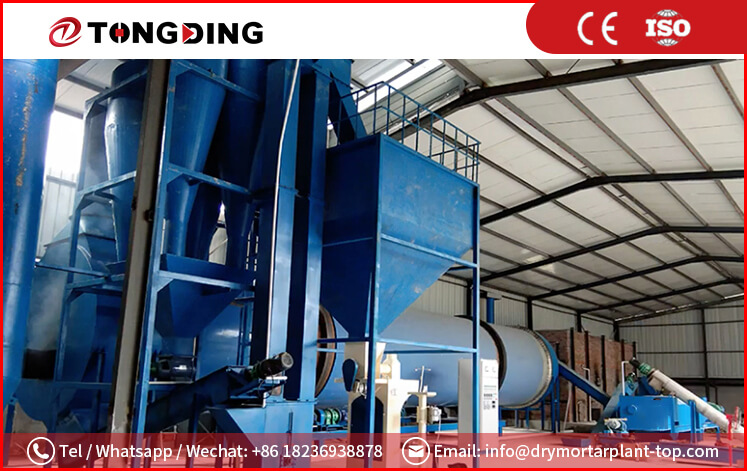
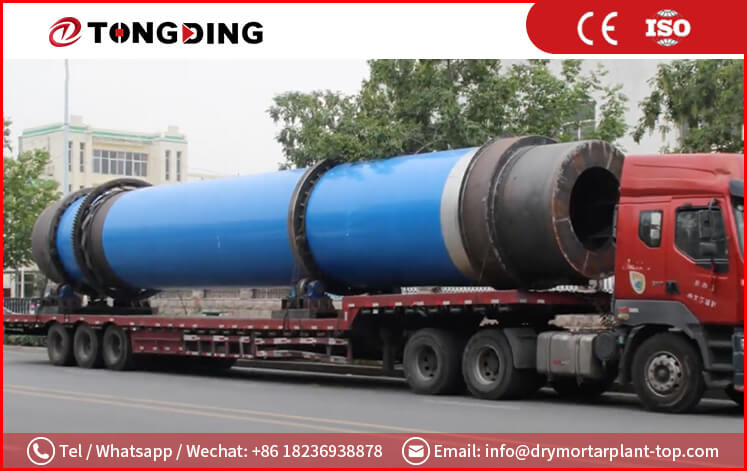
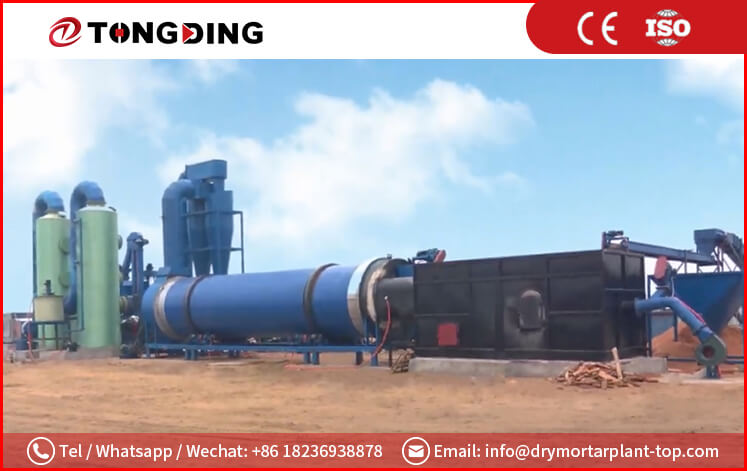
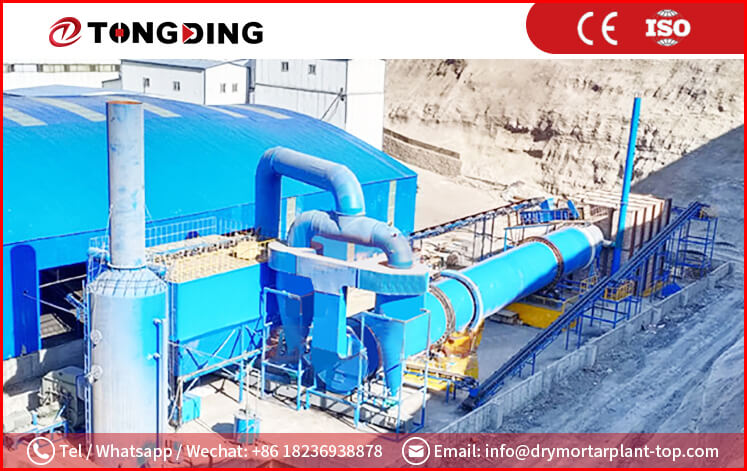
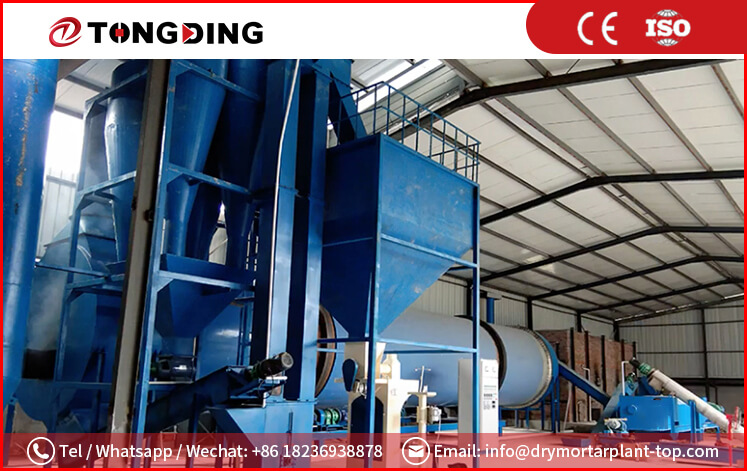
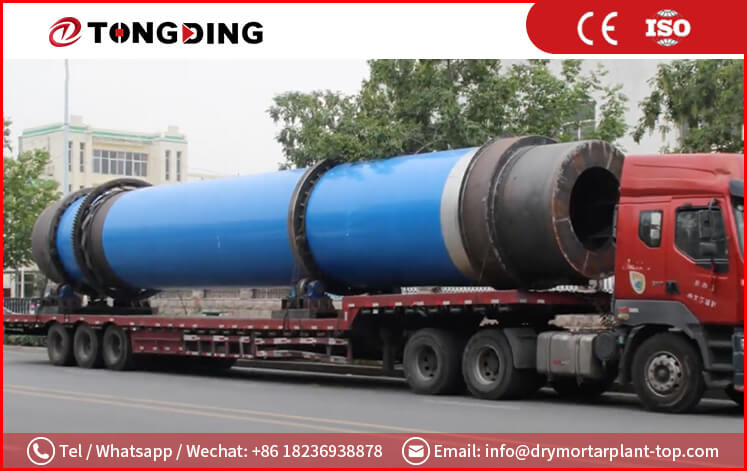
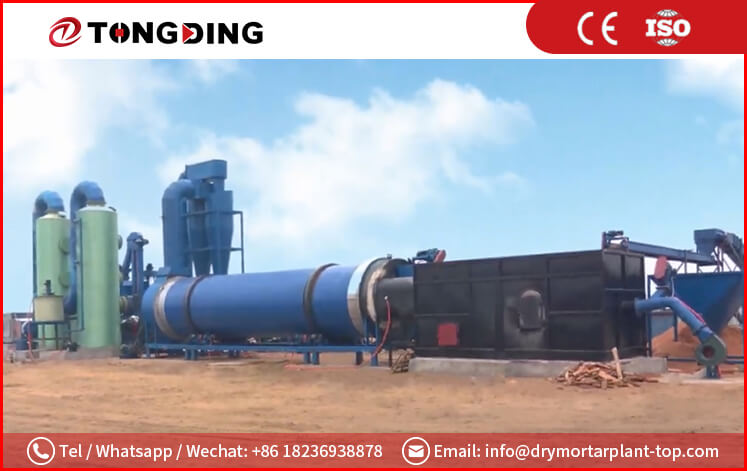
Coal Slime Rotary Dryer
Capacity: 5.4-80 t/h
Heat Source:Suitable for biomass, natural gas, diesel, coal, etc.
Application: Widely used for drying all kinds of coal, lignite, carbon coal, including anthracite, lean coal and poor lean coal, lean coal, coking coal, fat coal, air fertilizer coal, gas coal, etc.
Product Introduction
Coal slime is a waste residue generated during the coal washing process, and its high moisture content, viscosity, water content, and low calorific value make it difficult to be used industrially. TongDing company has developed a new generation of coal slime drying system through extensive technical research and practice, which can reduce the moisture content of the drying product to less than 15% and increase the calorific value to 2800-4200 kcal/kg, making it a good fuel for coal boilers. This equipment has mature technology, stable operation, and convenient operation and maintenance. The Coal Slime Dryer consists of a hot blast stove, belt feeding machine, drum dryer, belt discharging machine, induced draft fan, cyclone dust collector, bag filter (or wet dust collector), and operation control system. It uses a special dispersing device to break up the bonded slime and increase the contact area between the slime and the hot air, greatly improving the heat utilization rate. The dried slime can be directly used as fuel, which turns the coal slime into a valuable resource.
Layout Reference
Working Principle
The Coal drum dryer consists of a hot blast stove, belt feeding machine, drum dryer, belt discharging machine, induced draft fan, cyclone dust collector, bag filter (or wet dust collector), and operation control system. The equipment is used for downstream drying process, and operates in the following way:
1.Feeding area: Coal is rapidly exposed to high temperature and hot air to evaporate moisture. The material is then copied by a large-angle guide plate and enters the workspace.
2.Crushing beat cleaning area: This area is designed with a broken beat cleaning device. Wet mud is grabbed by the grating copy board and subjected to repeated breaking and beating until it is broken into 20-40 mm particles. This creates a curtain material state, increases the heat exchange area, improves the drying rate, and removes mud from the cylinder wall to prevent adhesion.
3.Main drying area: After processing in the previous two areas, the wet mud is in a granular and loose state. The material is copied by the feed plate to form a uniform state and undergoes full heat exchange with the hot air, leading to strong evaporation.
4.Pounding broken dry area: In this region, mud particles are repeatedly pounded and broken into 10-20 mm size, resulting in further moisture reduction.
Parameter
Model | Φ2.4x24m | Φ3.0x30m | Φ3.2x32m | Φ3.6x36m | Φ4.0x40m |
Inner diameter (mm) | 2400 | 3000 | 3200 | 3600 | 4000 |
Length (mm) | 24000 | 30000 | 32000 | 36000 | 40000 |
Power (kW) | 37 | 75 | 132 | 280 | 315 |
Inclination (°) | 0-5 | ||||
Shaft rotational speed (r/min) | 2-4 | 1-3 |
Inquiry
Please Feel free to give your inquiry in the form below. We will reply you in 24 hours.